相比于陸上風電,海上風電所處環(huán)境更為復(fù)雜,海洋大氣區(qū)高濕度、高鹽霧、長日照,浪花飛濺區(qū)干濕交替,水下區(qū)海水浸泡、生物附著等,腐蝕環(huán)境非常苛刻,這給海上風電設(shè)備的腐蝕防護帶來了嚴峻挑戰(zhàn)。海洋腐蝕不僅會縮短機組運營壽命,給海上風電機組帶來巨大安全隱患,而且也會大大增加海上風電的建設(shè)投資和運行維護成本。因此,防腐蝕是海上風電必須考慮的問題,防腐蝕設(shè)計也因此成為海上風電場設(shè)計的重要環(huán)節(jié)之一。前期文章“防腐技術(shù)在海上風電場中的應(yīng)用”主要對腐蝕環(huán)境、防腐方法和技術(shù)應(yīng)用等方面進行分析,本文重點介紹海上風電設(shè)備腐蝕機理及檢測方法。
海上風電設(shè)備腐蝕現(xiàn)狀
無論是海上風電還是其他海洋工程,海洋腐蝕以及生物污損都嚴重威脅著這些重大工程設(shè)施的安全運行。然而,目前大多數(shù)海洋工程結(jié)構(gòu)處于裸露或欠保護狀態(tài),海洋工程結(jié)構(gòu)安全堪憂,腐蝕損失巨大。如何保證各種海洋工程設(shè)施的耐久性和安全性,降低重大災(zāi)害性事故發(fā)生,延長這些重大工程設(shè)施的使用壽命,是當前我國海洋經(jīng)濟發(fā)展中需要迫切解決的關(guān)鍵性問題和共性問題。目前,我國海上風電防腐蝕方面主要存在以下問題:
我國海上風機腐蝕防護技術(shù)還不完善,缺少一套海上風電整體防腐的體系標準。
防腐設(shè)計基礎(chǔ)相對薄弱,相關(guān)人員對海上風電設(shè)備防腐認知不足。所有產(chǎn)品的防腐設(shè)計都應(yīng)當依據(jù)產(chǎn)品自身服役環(huán)境的特點來制定對應(yīng)的產(chǎn)品防腐方案。海上風電設(shè)備防腐設(shè)計的重點在于其防腐環(huán)境特別惡劣,防腐技術(shù)要求高,且難以進行二次維護。因而,在對海上風電設(shè)備進行防腐設(shè)計時,必須對其服役環(huán)境進行具體了解,并且掌握所使用材料的各種物化性能(耐老化性、耐鹽霧性、導(dǎo)電性等),掌握一些基本的產(chǎn)品防腐結(jié)構(gòu)設(shè)計方面的知識,才能夠進行合理而可靠的產(chǎn)品防腐設(shè)計。
海上風電防腐蝕是一個系統(tǒng)工程,從涂層體系配套、涂料選用、表面處理、涂裝施工到安裝運行階段,都需要進行嚴格控制。現(xiàn)階段,國內(nèi)海上風電配套體系方案少,國內(nèi)設(shè)備供應(yīng)商對海上風電設(shè)備涂裝工藝的積累不足,安裝、運營單位對設(shè)備的維護和保養(yǎng)的經(jīng)驗欠缺等,這些因素都會影響到海上風電設(shè)備的防腐性能。
海上風電設(shè)備腐蝕機理
海洋環(huán)境是腐蝕性最為嚴酷的自然環(huán)境。海水是一種具有很強腐蝕性的電解質(zhì)溶液,含有大量鹽類, 包括氯化鈉及含有鉀、溴、碘等元素的鹽類。海水中溶解有氧氣、氮氣、二氧化碳等氣體,而其中的氧氣是引起海水中碳鋼、低合金鋼等金屬結(jié)構(gòu)物腐蝕的重要影響因素。表層海水氧氣是飽和的,約為8mg/L,腐蝕性更強。海水溫度呈周期性變化,一般來說,鋼鐵等的腐蝕速度會隨著海水溫度的升高而增加。另外,海水中含有豐富的氧微量元素和營養(yǎng)鹽類等,這為海洋生物的生存和繁殖提供了必要條件。而海洋生物的存在則會影響金屬材料的腐蝕行為與機制。
海水與空氣接觸面積大、對流充分,在海浪的不斷攪拌下,氧氣飽和、濕度極大,加快了海上風電設(shè)備的腐蝕速率。風電機組“有風發(fā)電、無風停機、超風速急停”的不均勻運轉(zhuǎn)模式會產(chǎn)生高頻交變應(yīng)力的疲勞荷載作用,這導(dǎo)致了風電機組腐蝕疲勞加速,嚴重影響了海上風電機組的使用壽命。
海上風電場的防腐措施盡管可以在很大程度上參考海洋平臺現(xiàn)有的防腐經(jīng)驗,但是二者之間也有較大不同。海上風電場是無人居住的,并且嚴格限制人員的接近。海洋平臺是有人居住的,海洋平臺上的防腐涂層檢查和維修可更容易且有計劃地進行,受到腐蝕時可以隨時修補。而海上風電場很難做到這一點,維修費用極高,后續(xù)維護費用是其成本的7倍以上。因此,應(yīng)當更加重視海上風電機組的鋼結(jié)構(gòu)腐蝕,特別是外露于海洋大氣和飛濺區(qū)中的部位。一般情況下,大氣區(qū)結(jié)構(gòu)件采取涂料保護或熱噴涂金屬保護,如大氣區(qū)鋼結(jié)構(gòu)一般采用環(huán)氧富鋅底漆(含鋅≥80%)、環(huán)氧云鐵漆、聚氨酯面漆(或者聚氨酯+氟碳雙重面漆)3層涂層體系;飛濺區(qū)鋼結(jié)構(gòu)一般采用玻璃鱗片漆、環(huán)氧耐磨漆雙層涂層體系;全浸區(qū)一般采用玻璃鱗片漆、環(huán)氧厚漿漆雙層涂層體系,并采取犧牲陽極進行協(xié)同防腐。
此外,目前風電行業(yè)往往主要關(guān)注海上風電結(jié)構(gòu)件腐蝕,對電器設(shè)備腐蝕問題缺乏系統(tǒng)性認識和解決方案,一般來說,海上風電機組的關(guān)鍵電器設(shè)備更易受鹽霧的侵蝕,電器設(shè)備故障率會明顯上升。考慮到海上風電電器設(shè)備的種類繁多,重點應(yīng)從改善電器設(shè)備服役環(huán)境條件著手,主要措施包括:在提高機艙及塔筒密封性的同時,應(yīng)增加空氣凈化防腐系統(tǒng),去除塔筒、機艙或者集裝箱內(nèi)部的鹽霧,并且降低空氣的濕度。依據(jù)塔筒、機艙或者集裝箱內(nèi)部實際空間的大小,可以確定所需的空氣凈化防腐系統(tǒng)凈化風量;此外,鹽霧凈化處理應(yīng)去除 90%以上海洋環(huán)境中獨有的腐蝕性鹽分顆粒。
腐蝕檢測方法
為了更好地分析海上風電設(shè)備的腐蝕情況,以某海上風電場的風機及升壓站的評估結(jié)果為例,從涂層使用狀態(tài)和完整性、陰極保護及犧牲陽極使用狀態(tài)檢測、可溶性鹽分含量檢測等方面,探討海上風機、升壓站的腐蝕檢測分析方法。
1、涂層使用狀態(tài)和完整性
通常采用的檢查方法一般為在自然光照射下,檢查人員目視檢查涂層變色、粉化、開裂、起泡、長霉、生銹和剝落等缺陷,對涂層表面目視可見的均勻破壞采用破壞的變化程度進行評級,非連續(xù)性或其局部不規(guī)則破壞采用破壞數(shù)量進行評級,具體評級參照《GB/T 30789 色漆和清漆涂層老化的評價》。此外,依據(jù)能源部標準《NB/T 31006-2011 海上風電場鋼結(jié)構(gòu)防腐蝕技術(shù)標準》要求,對鋼管樁干膜厚度進行測量,評價標準為:所有測點干膜厚度的平均值應(yīng)不低于設(shè)計干膜厚度,所有測點的干膜厚度應(yīng)不低于設(shè)計干膜厚度的80%,80%以上測點的干膜厚度應(yīng)達到設(shè)計干膜厚度的要求。
以往海上風電風機設(shè)備腐蝕測量多是在鋼管樁、塔筒外壁、塔筒內(nèi)壁各選擇若干測區(qū)進行測量,每個測區(qū)采用五點取樣法進行測試,最終計算所有測試結(jié)果的算術(shù)平均值作為該測區(qū)的平均干膜厚度。
通過對過往風機和海上升壓站在海洋大氣區(qū)、海水飛濺區(qū)、潮差區(qū)的腐蝕狀態(tài)進行檢查時可以發(fā)現(xiàn),風機和海上升壓站鋼管樁水上部分防腐涂層表面狀況大部分良好,未發(fā)現(xiàn)明顯的變色、粉化、裂紋、起泡現(xiàn)象,部分風機鋼管樁局部有小面積破損、脫落和銹蝕情況;風機附屬結(jié)構(gòu)(爬梯、平臺、船靠等)局部腐蝕比較嚴重,很多腐蝕都是由于初期建設(shè)階段涂層損壞未及時修復(fù)引發(fā)的,且多數(shù)鋼管樁潮差區(qū)被海生物覆蓋。具體見圖1。
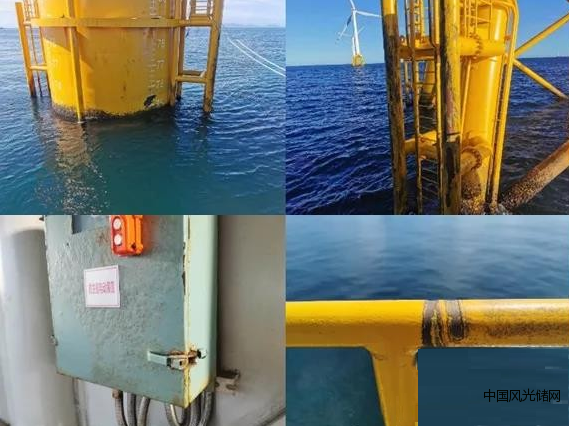
圖1 風機鋼管樁及附屬結(jié)構(gòu)局部腐蝕及海生物附著圖片
涂層厚度方面,多是根據(jù)風電場提供的風機基礎(chǔ)設(shè)計信息,檢測的位置多為導(dǎo)管架鋼樁表面涂層、塔筒內(nèi)壁涂層、塔筒外壁涂層等。一般而言,若基礎(chǔ)鋼管樁涂層干膜厚度小于原設(shè)計厚度,且低于原設(shè)計厚度的80%,便已不符合標準要求,說明風機基礎(chǔ)鋼管樁涂層厚度較差。不過,還需結(jié)合現(xiàn)場的檢測情況做最終判斷。很多時候比設(shè)計值偏小的涂層多為修復(fù)過后的的涂層,主要原因應(yīng)該是吊裝施工過程中涂層損壞之后的修復(fù)沒有嚴格按照涂層設(shè)計要求進行。
此外,若塔筒內(nèi)壁不存在損壞修補過程,而且使用時間也比較短,測量干膜厚度基于等于出場干膜厚度。這說明,塔筒內(nèi)壁的厚度并沒有經(jīng)過嚴格檢測,未在確保合格后即出廠。表1為某風機設(shè)備抽取的的部分測量數(shù)據(jù)實例。
表1 風機升壓站涂層厚度測量結(jié)果
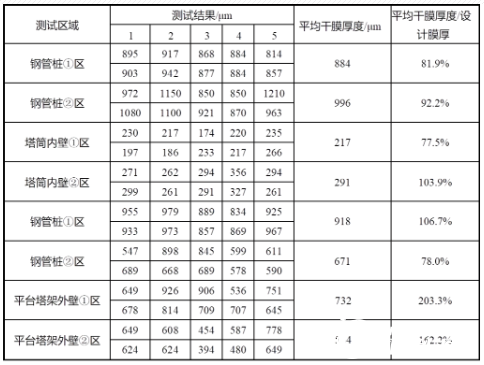
2、陰極保護及犧牲陽極使用狀態(tài)檢測
電位檢測也同樣很重要,一般采用銅/飽和硫酸銅參比電極、高阻抗數(shù)字萬用表,自水面向下取平均水深約5m范圍內(nèi)進行檢測。檢測共選取若干方位,逆時針排序檢測,每隔約120°為一個檢測方位,每個檢測方位以電極接觸水面開始檢測,向下放電極每間隔約1m記錄一個測量值,檢測示意圖見圖2。
按照規(guī)范規(guī)定,采用犧牲陽極保護時,鋼質(zhì)港工設(shè)施最小保護電位應(yīng)達到-0.85V(相對銅/飽和硫酸銅參比電極,以下同),最大保護電位不超過-1.10V。
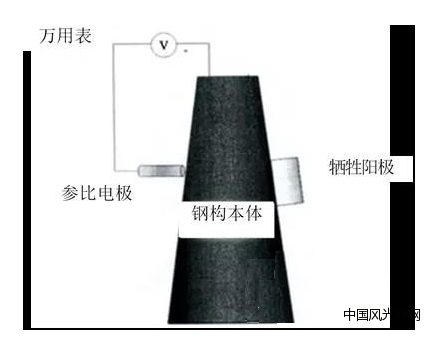
圖2 陰極保護電位檢測示意圖
犧牲陽極使用狀態(tài)檢測由專業(yè)潛水檢測人員攜帶攝像設(shè)備、清理工具、測量工具,潛水員用鋼絲刷、斧頭或其他工具清除陽極和焊縫表面的腐蝕產(chǎn)物及其他附著物,露出陽極和焊接部位的本體表面。
犧牲陽極使用狀態(tài)檢查時,需要對每臺風機隨機抽取的犧牲陽極進行探摸檢查和測量尺寸。過往檢查就曾發(fā)現(xiàn),多數(shù)犧牲陽極表面均會被海生物覆蓋,需用工具才可清除,犧牲陽極表面溶解較好。陽極焊腳焊接情況良好。如果設(shè)備使用時間較短,那么陽極塊整體的損耗一般不大,大部分的測量數(shù)據(jù)基本都會在設(shè)計值或之上,不太會出現(xiàn)損耗較大的犧牲陽極塊,剩余使用壽命基本與設(shè)計使用壽命一致。
此外,對清理干凈的犧牲陽極本體和鐵腳部位還需要求進行錄像檢測,并隨機抽取每臺風機的若干個犧牲陽極用軟尺對陽極上、中、下不同位置的周長及陽極長度進行測定。船上檢測人員進行實時監(jiān)測和錄像操作,并測量陽極表面局部蝕坑的深度。船上檢測人員記錄陽極表面狀況,記錄檢測數(shù)值。
3、可溶性鹽分含量檢測
通常根據(jù)《GB/T 18570.6-2011 涂覆涂料前鋼材表面處理 表面清潔度的評定試驗 第6部分:可溶性雜質(zhì)的取樣Bresle法》,目前多是采用Bresel法測試現(xiàn)場各塔筒內(nèi)表面含鹽量,并隨機抽取一定數(shù)量風機測試機艙內(nèi)表面、升壓站開關(guān)室和塔筒外壁進行含鹽量檢測,其原理為測量所有水溶性鹽離子的電導(dǎo)率,并將其換算成單位面積上的NaCl含量。目前國內(nèi)、國際對涂層表面的可溶性鹽分無統(tǒng)一的數(shù)值標準,業(yè)界公認的可溶性鹽分的允許值為100mg/m2, 某不同濃度可溶性鹽分對涂層的影響見表2。
表2 可溶性鹽分含量對涂層的影響
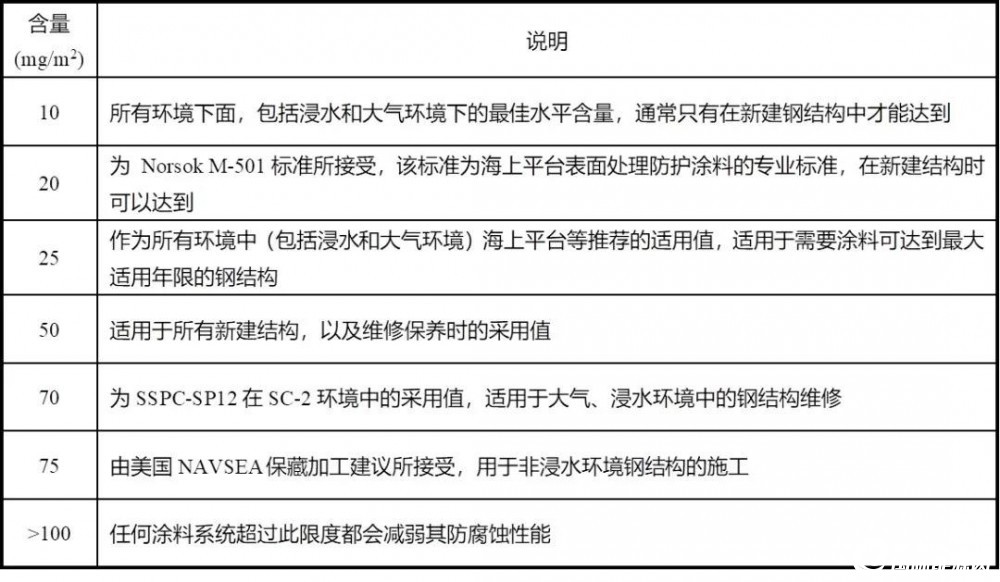
通過以往檢測結(jié)果可以發(fā)現(xiàn)一些規(guī)律,升壓站從一層逐漸往上含鹽量是有明顯降低的趨勢,風機從塔筒底部內(nèi)壁至機艙也有該趨勢,可能是因為升壓站一層及風機塔筒底部人員活動頻繁,相應(yīng)的設(shè)備間、塔筒門的開關(guān)頻繁,與海洋大氣接觸較多,表面鹽分沉積增多。塔筒外壁雖然一直處于海洋大氣環(huán)境中,測試結(jié)果低于絕大部分的室內(nèi)測試數(shù)據(jù)。
結(jié)語
隨著我國海上風電開發(fā)和利用的速度加快,迫切需要結(jié)合我國的實際情況深入開展海上風電機組的腐蝕防護等關(guān)鍵性技術(shù)研究,同時加快海上風電機組腐蝕與防護技術(shù)的應(yīng)用探索,從而助力海上風電產(chǎn)業(yè)的健康發(fā)展。